In the domain of the automotive industry, vehicle defects present an intricate and highly consequential issue. Corporations find themselves at the intersection of legal obligations, ethical responsibilities, and business considerations. How they respond to these defects, the subsequent recalls, and the potential legal implications create a complex narrative. While it’s clear that corporations must be held accountable for their products, the extent of this liability and its impact on the automotive industry is a topic worthy of further exploration.
Understanding Vehicle Defects
In the complex world of automotive manufacturing, vehicle defects represent an inevitable, albeit unfortunate, reality. These defects, variably ranging from minor inconveniences to severe safety hazards, pose significant challenges not just for manufacturers, but also for consumers and regulatory authorities.
A thorough understanding of vehicle defects necessitates an in-depth look at two key areas – vehicle safety and defect reporting. From a vehicle safety perspective, defects could compromise the functionality of critical components such as brakes, airbags, and seat belts, thereby increasing the risk of accidents. Additionally, defects could also impact non-critical components, leading to diminished performance and overall user experience.
Defect reporting, on the other hand, is a systemic process that facilitates the identification, analysis, and rectification of defects. This process, mandated by law in numerous jurisdictions, plays an essential role in ensuring that defects are promptly addressed to minimize their potential impact on vehicle safety. It also contributes to the ongoing improvement of automotive manufacturing processes by highlighting areas of concern, thereby paving the way for proactive measures to prevent the recurrence of similar defects in the future.
The Role of Vehicle Manufacturers
Having established the nature and implications of vehicle defects, it’s pertinent to focus on the responsibilities of vehicle manufacturers in this scenario. Manufacturers play a critical role in guaranteeing consumer safety, as the quality of the vehicles they produce depends largely on their adherence to strict manufacturing standards.
Vehicle manufacturers are responsible for designing, producing, and testing vehicles before they are introduced to the market. They must comply with established manufacturing standards, which dictate the quality of materials used and the processes followed during production. These standards are set to guarantee the production of safe, reliable, and durable vehicles.
Moreover, manufacturers are expected to conduct rigorous testing of vehicles to identify and rectify any defects before they reach consumers. Failure to do so not only risks consumer safety, but also exposes the company to potential legal actions and reputational damage. In the event of defects being discovered post-purchase, manufacturers are typically required to issue recalls to rectify the problem at no cost to the consumer.
Legal Framework for Vehicle Defects
The legal landscape surrounding vehicle defects is a complex web of rules and regulations designed to protect consumers and hold manufacturers accountable. This framework is formed by a combination of federal and state laws that stipulate legal standards for vehicle safety. These laws mandate that manufacturers adhere to strict regulatory compliance, with a failure to do so potentially leading to severe consequences.
Federal laws such as the National Traffic and Motor Vehicle Safety Act empower government bodies to set safety standards for vehicles and vehicle equipment. This Act also obliges manufacturers to recall vehicles that have safety-related defects or do not meet federal standards. At the state level, Lemon Laws provide remedies to consumers for vehicles that repeatedly fail to meet certain standards of quality and performance.
Regulatory compliance is an ongoing process that requires manufacturers to constantly monitor their operations and products. They must guarantee they meet evolving legal standards, adapt to new legislation, and respond appropriately to any identified defects. This legal framework aims at guaranteeing the production of safe vehicles, reducing accidents caused by defects, and holding corporations accountable for any lapses in safety.
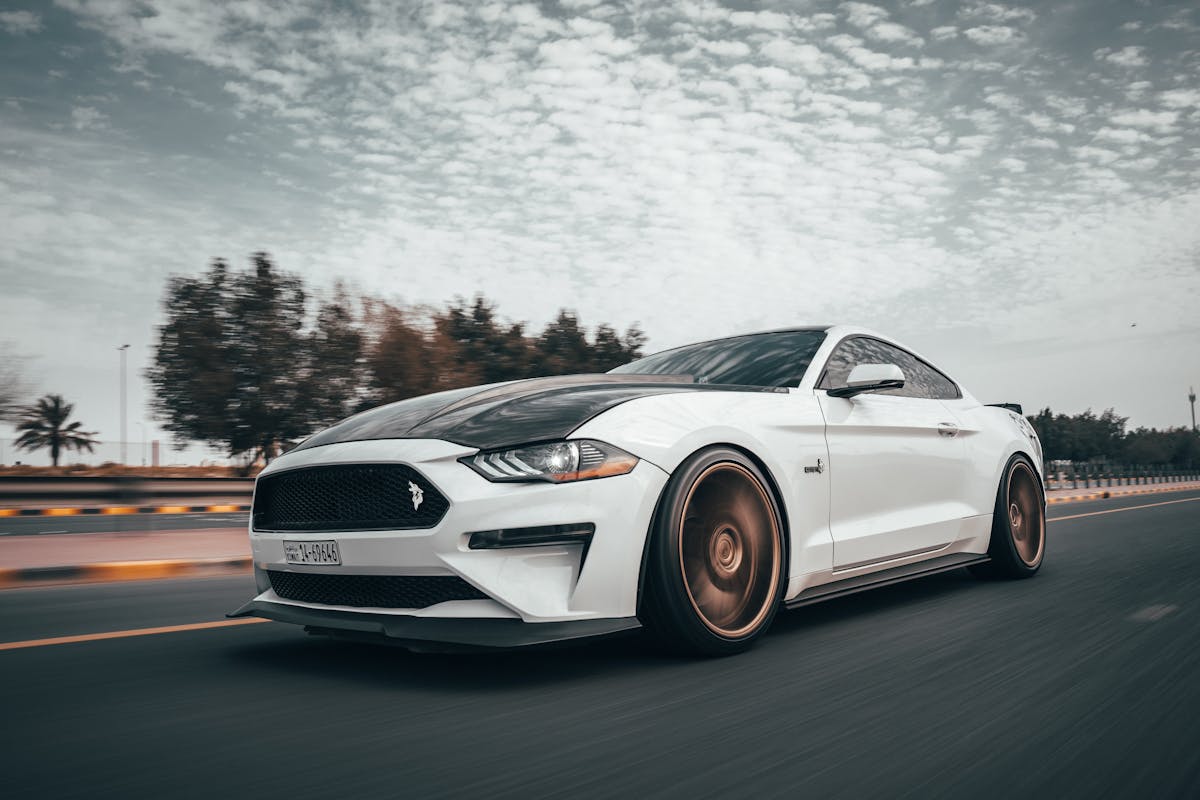
Case Studies of Notable Defects
Despite the established legal framework designed to guarantee vehicle safety, there have been notable instances where corporations failed to meet these standards, resulting in severe vehicle defects. These incidents offer invaluable lessons for future prevention and they underscore the importance of corporate diligence in ensuring product safety.
Below are five key examples:
- The Toyota Recall: In 2009, Toyota recalled more than 9 million vehicles due to uncontrolled acceleration issues, a defect linked to several accidents and fatalities.
- The Ford Firestone case: This infamous defect involved tire tread separation in Ford Explorers fitted with Firestone tires, leading to multiple rollovers and casualties.
- General Motors Ignition Switch Failure: In 2014, GM recalled 800,000 cars due to faulty ignition switches blamed for at least 124 deaths.
- Takata Airbag Scandal: Faulty airbag inflators led to the recall of tens of millions of vehicles worldwide and at least 15 deaths in the U.S. alone.
- Volkswagen Emission Scandal: VW was found guilty of installing software to cheat emission tests in 2015, impacting 11 million cars globally.
Each case brings forth unique circumstances and consequences, yet all underscore the critical need for stringent safety measures and quality control in vehicle manufacturing.
Corporate Responsibility and Accountability
Corporations bear a significant level of responsibility when it comes to the safety of their products, particularly in the vehicle manufacturing industry. With the imperative of maintaining public safety, these corporations are expected to follow stringent ethical considerations and uphold transparent practices.
Ethical considerations compel corporations to guarantee the highest standards of safety, irrespective of the costs involved. This includes undertaking rigorous testing of vehicle parts and systems, addressing potential defects proactively, and guaranteeing effective recall processes if defects are identified post-production. Negligence or deliberate oversight in these areas is not only ethically reprehensible but also entails substantial corporate liability.
Transparency practices, on the other hand, involve the candid disclosure of information related to product safety, manufacturing processes, and identified defects. A transparent corporate culture fosters trust among consumers, stakeholders, and regulatory bodies. It also serves as a deterrent against the concealment of defects and the provision of misleading information.
The Consequences of Ignoring Defects
What might be the repercussions if a corporation chooses to ignore or conceal defects in their vehicles? Companies that choose this path potentially face grave consequences, not only from a financial standpoint but also concerning the erosion of consumer trust.
Financially, corporations may be hit with substantial penalties, litigation costs, and compensation payments. The financial repercussions can be crippling, leading to losses in the billions.
The loss of consumer trust is an equally severe consequence. Once customers believe a company is willing to risk their safety to save money, regaining their confidence is an arduous task, often taking years and significant investment.
Here are five potential outcomes if a corporation ignores or conceals vehicle defects:
- Financial penalties imposed by regulatory bodies
- Costly lawsuits filed by affected consumers
- Significant compensation payouts to victims
- Irreparable damage to brand reputation
- Loss of consumer trust leading to decreased sales
Every defective product that reaches the market symbolises a broken promise to the consumer. The implications are far-reaching, affecting not only the corporation’s bottom line but also its standing in the eyes of the public. The consequences of ignoring defects are severe and long-lasting.
Managing Recalls and Replacements
Maneuvering the complex process of initiating and managing recalls and replacements is a critical aspect of corporate responsibility when vehicle defects are discovered. Effective recall strategies must be in place to swiftly identify faulty vehicles and prevent them from causing harm. This requires an extensive system of tracking and monitoring that can detect anomalies and trigger an immediate response.
The replacement processes are equally important, with their own set of challenges. They involve not only the logistical aspects of replacing defective parts or entire vehicles, but also the financial and reputational costs. Companies must efficiently manage large-scale replacements to minimize disruption for consumers and maintain public confidence. They must also guarantee that the replaced parts or vehicles are of high quality to avoid repeating the same mistakes.
Both recall strategies and replacement processes are essential components of corporate liability management in situations of vehicle defects. Though challenging, their successful implementation can greatly reduce corporate risk and protect consumer safety. They require diligent planning, rigorous execution, and continuous improvement based on feedback and learning from past defects. This is not just a regulatory requirement, but a corporate necessity in today’s consumer-centric market.
Preventive Measures for Vehicle Defects
In the domain of automotive manufacturing, implementing preventive measures for vehicle defects is of paramount importance. These measures aim to guarantee the production of safe, reliable vehicles and lower the risk of costly recalls or potential lawsuits. A well-structured preventive strategy should encompass regular preventive inspections and adherence to safety protocols.
- Regular preventive inspections can identify potential issues before they escalate into severe defects. This proactive approach can save both time and resources in the long run.
- Safety protocols, including rigorous testing of vehicle systems and components, are a necessity in the manufacturing process. These protocols should be updated regularly to reflect technological advancements and emerging risks.
- Employee training should be prioritized to guarantee all staff understand and follow the established protocols.
- Quality control mechanisms should be robust and capable of detecting any deviations from the set standards.
- Finally, feedback loops should be implemented. They allow for continuous improvement by identifying recurring problems and formulating strategies to eliminate them.
These preventive measures not only mitigate the risk of vehicle defects but also contribute to a culture of safety and quality in the automotive industry. The onus lies with corporations to implement and uphold these measures to avoid liability.
Frequently Asked Questions
What Are the Consumer Rights in Vehicle Defect Cases?
In vehicle defect cases, consumers have the right to warranty claims and vehicles meeting safety standards. They can demand repairs, replacements, or refunds when their vehicles do not meet the advertised or implied standards.
How Can an Individual Prove a Defect Caused an Accident?
To prove a defect caused an accident, an individual must present defect evidence such as expert analysis, recall notices, or manufacturer’s admissions. Establishing a clear causal link between the defect and accident is critical for a successful claim.
How Does Insurance Factor Into Vehicle Defect Issues?
Insurance coverage plays a pivotal role in vehicle defect issues. It often becomes the primary source of compensation in liability claims, providing financial recourse for damages caused by vehicle defects, subject to policy limits and conditions.
What Is the Process to File a Lawsuit Against a Vehicle Manufacturer?
To file a lawsuit against a vehicle manufacturer, one initiates the litigation process by retaining legal representation, filing a complaint, and proving manufacturer accountability for the defect causing harm or financial loss.
Can Vehicle Defects Lead to Class Action Lawsuits?
Yes, vehicle defects can indeed lead to class action lawsuits. When vehicle recalls occur due to manufacturing faults, it raises product liability issues, which can collectively affect a large group of consumers, prompting class action suits.